CTS SOLUTION QUALITY CONTROL
CTS SOLUTION has been a thriving precision stamping manufacturer and progressive die design service company for over 15 years. Our success is due to our complete attention to quality. We are ISO 9001, ISO 14001 Certified to better serve our clients.
Production tolerances of +/-0.002mm as standard are the condition for the high performance of our stamping tools, our capacity enables the quick production of cutting elements for the tool. Highly trained employees operate modern machines for Profile Grinding, Wire-EDM, EDM, HSC Milling, and Grinding process.
TRAINING MATRIX
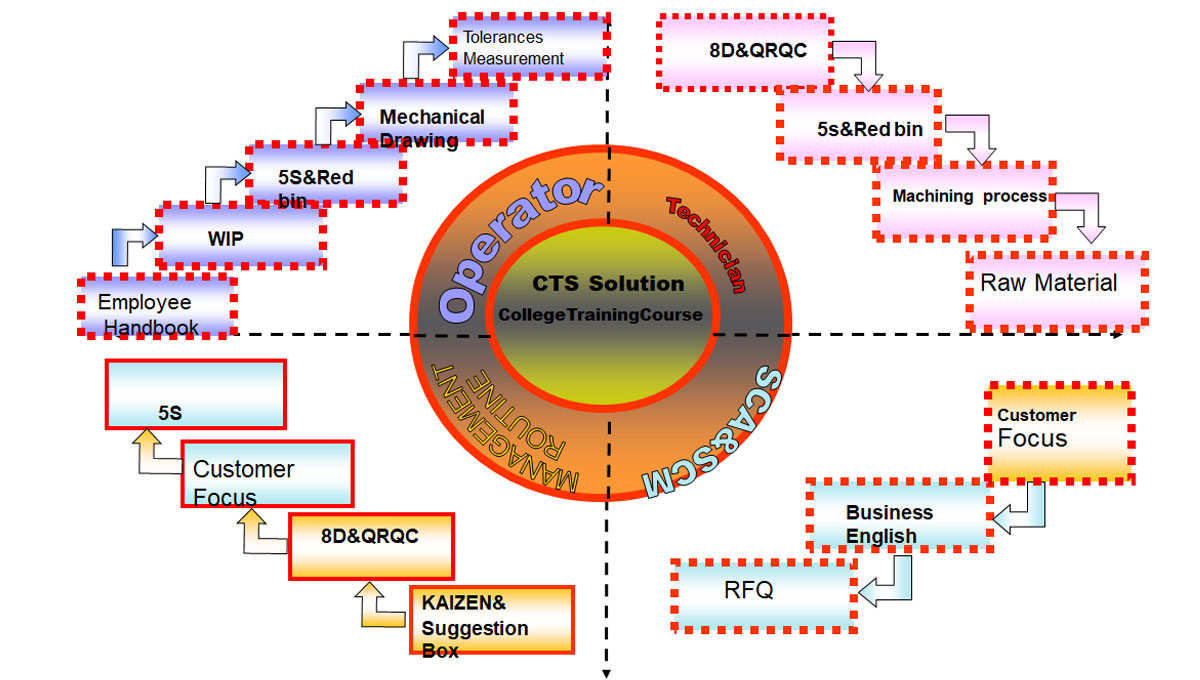
CTS SOLUTION QUALITY CONTROL MANAGEMENT
1. Before mass production, the QA will test the First Article Inspection in each batch.
2. We have measurements devices made from Japan such as YVM, microscope, projector.
3. We have the complete staffing architecture including IQC, IPQC, QE, and OQC.
4. We will follow the CPK management to inspect products.
5. All batch products have unique part No. If there is a quality problem, the product can be tracked by part No.
6. We will train our employees every month to help them to improve their inspection skills.
If you have a chance to do a factory audit or entrust a third party to do, welcome to our factory at any time.
Japan High-speed CNC
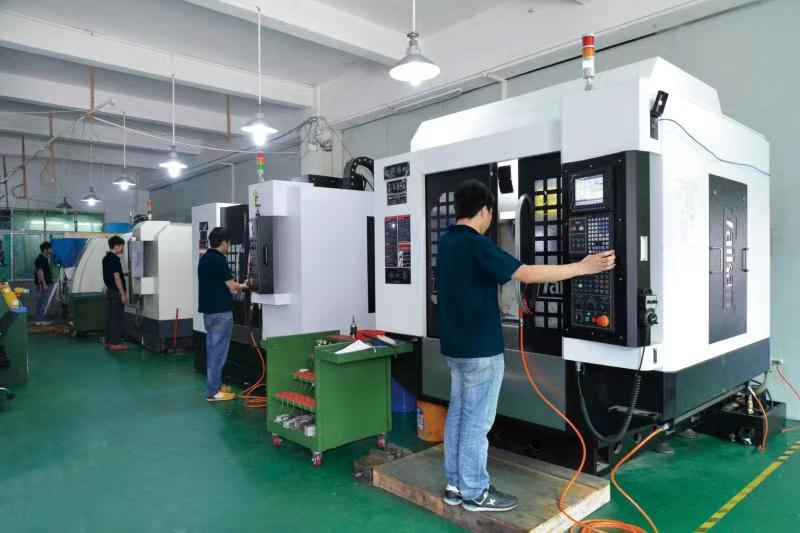
Japan Precision WEDM
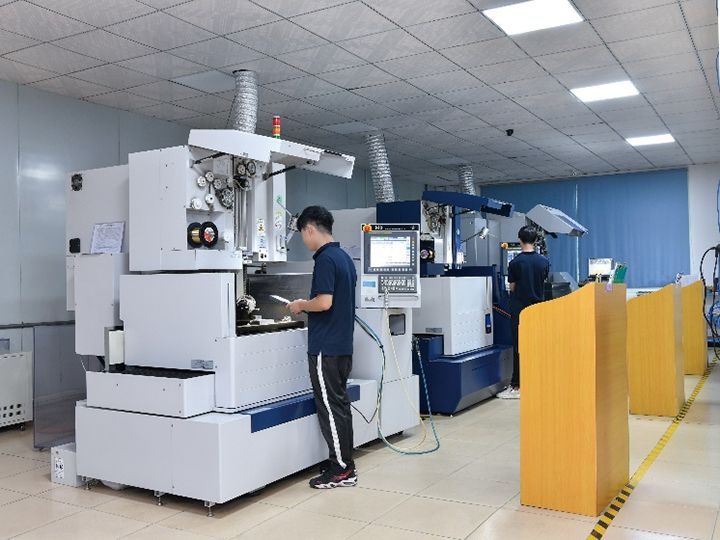
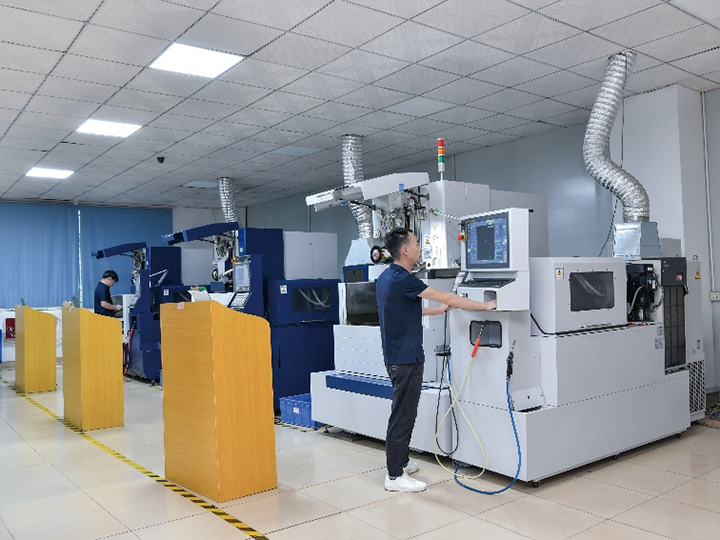
CLIMATE CONTROL IN WORKSHOP.
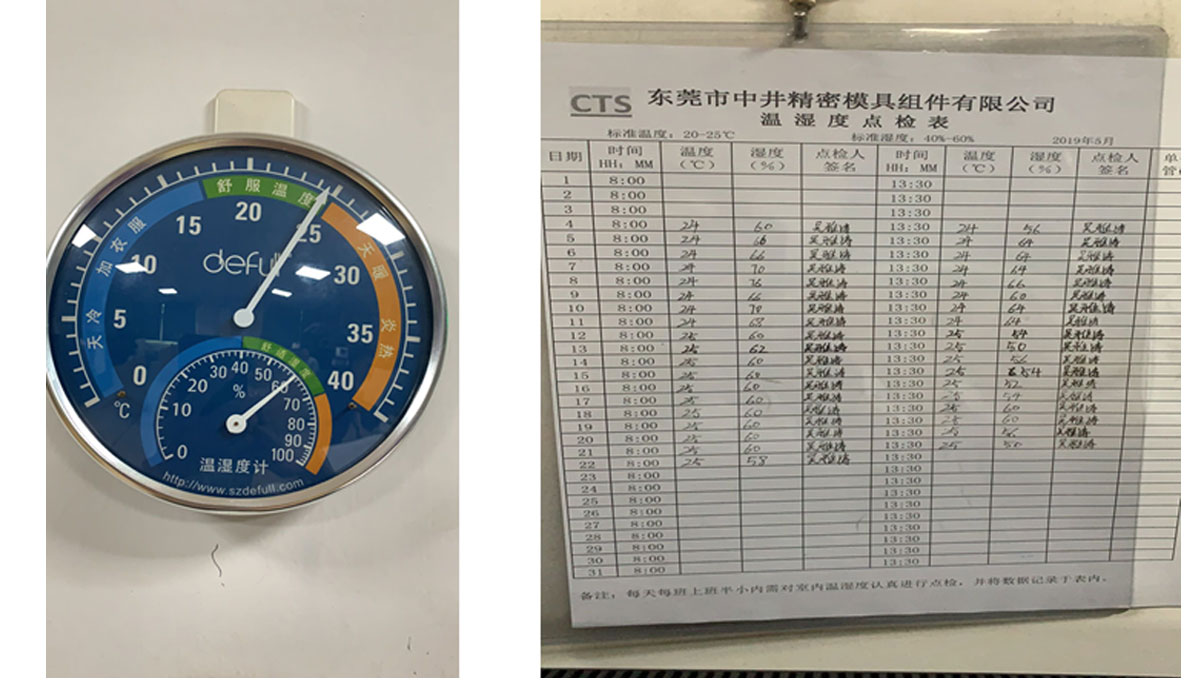
CTS SOLUTION QUALITY CONTROL PROCESS
Every process is subjected to our high-quality standards. CTS SOLUTION offers the following quality assurance programs to meet the strictest of quality standards:
supplying qualifications review |
supplier basis survey |
supplier quality environmental protection system review |
supplier evaluation form; quality environmental contract |
supplier quality and service supervision review
|
supplier quality, delivery, service month score table |
incoming quality inspection |
feed inspection report |
MATERIAL AND PRODUCT QUALITY INSPECTION
Then will do a series of material inspections, like incoming inspection, process inspection, outgoing inspection, inventory retest, and so on, make sure raw material is the same: meet customer’s demand with high quality when entering our factory, sampling, and till delivery the parts.
Quality Management Flow Chart
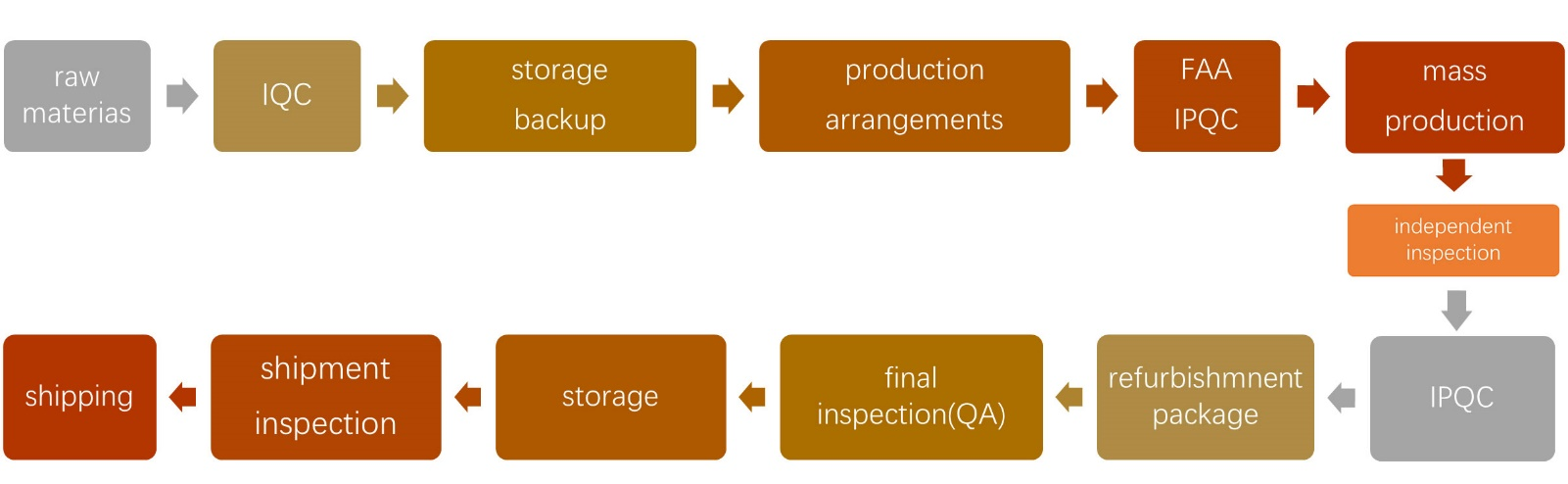
AFTER SERVICES
Timely conversion of customers’ latest standards of quality and environmental.
Customer system audit and product audit cooperate and support.
Management and maintenance of customer property.
Handling and tracking customer complaints.
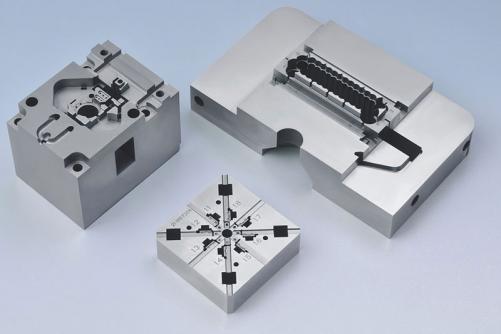
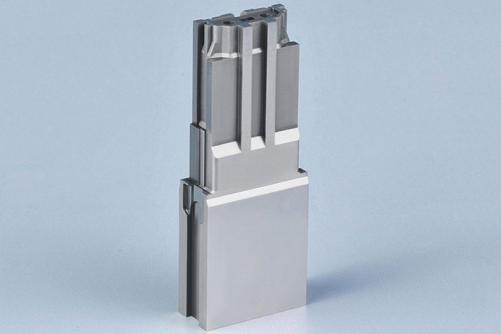